2025 Outeur: Howard Calhoun | [email protected]. Laas verander: 2025-01-24 13:10
Vandag word 'n groot aantal verskillende goed, onderdele, ens. van staal gemaak. Dit vereis natuurlik 'n groot hoeveelheid bronmateriaal. Daarom gebruik die aanlegte lank reeds die metode van deurlopende giet van staal, gekenmerk deur die belangrikste kenmerk - hoë produktiwiteit.
Noodsaaklike toerusting vir werk
Tot op hede is verskeie installasies vir die giet van staal op hierdie manier bekend, en hulle word as UNRS afgekort. Aanvanklik is 'n vertikale-tipe installasie ontwikkel en in produksie gestel, geleë 20-30 meter onder die vlak van die werkswinkelvloer. Maar later het die begeerte om die verdieping van die vloer te laat vaar die hoofmotor vir die ontwikkeling van hierdie installasies geword. Dit het gelei tot die ontwikkeling en implementering van toring-tipe deurlopende gietaanlegte. Die hoogte van hierdie installasies was 40 m. Hierdie weergawe van die masjien is egter om twee redes nie algemeen gebruik nie. Eerstens, bouso 'n eenheid in die werkswinkel is nogal problematies en moeisaam. Tweedens het nog meer probleme met die werking daarvan ontstaan.
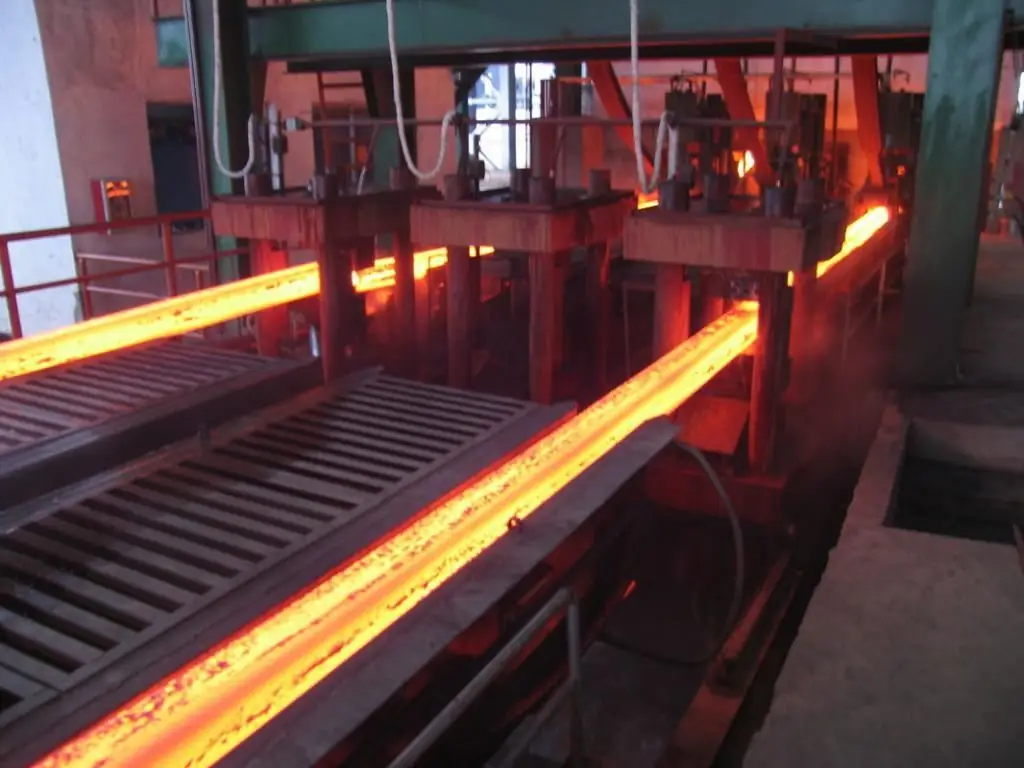
Geboë en radiale installasies
Met verloop van tyd is deurlopende giet van staal oorgeplaas na werk met vertikale buigmasjiene. Die belangrikste kenmerk is die buiging van die ingot wat na die asse uitkom met 90 grade. Daarna is 'n spesiale reguitmaakmeganisme in die installasie gebruik om die steen reguit te maak, en eers na hierdie stadium het die snywerk plaasgevind. Deurlopende giet van staal op sulke toerusting het om een of ander rede nie baie gewild geword nie. Eerstens het die buiging dit natuurlik moontlik gemaak om die hoogte te verminder, maar terselfdertyd die dwarssnit van die ingot self ernstig beperk. Hoe meer dit nodig was om 'n gedeelte van die materiaal te verkry, hoe groter moes die buiging wees, wat beteken dat die hoogte weer toegeneem het. Tweedens is die buigmasjiene met selfs groter probleme in die staalwinkels geplaas as die vertikales.
Vandag word installasies vir deurlopende giet van radiale staal al hoe meer gewild. Op so 'n eenheid word die staaf in die vorm gevorm en verlaat dit langs dieselfde boog waarlangs dit dit binnegekom het. Daarna sal dit reguit gemaak word deur 'n trek-korrekte meganisme. En dan kan jy reeds begin om die staaf in spasies te sny. Dit is hierdie ontwerp wat in die praktyk die mees rasionele blyk te wees om die vloei van goedere in die staalwinkel te organiseer.
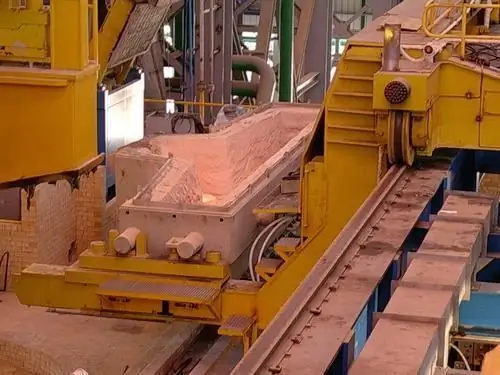
Waar begin uitsaaiery
Tegnologie van deurlopendestaal giet is 'n taamlik ingewikkelde proses. Dit is egter billik om te sê dat die beginsel dieselfde bly ongeag die produksie-opstelling wat gebruik word. Jy kan die tegnologie oorweeg deur die voorbeeld van 'n vertikale UNRS te gebruik.
Die masjien word voorsien van 'n skeplepel om staal deur 'n spesiale hyskraan te gooi. Daarna vloei die staal in die opvangbak, wat 'n prop het. Vir enkelstrengmasjiene sal daar een prop wees, vir multistrengmasjiene sal daar een prop per stroom wees. Daarbenewens het die opvangbak 'n spesiale rooster om die slak vas te hou. Van die opvangbak sal die staal in die vorm vloei en deur 'n doseerglas of 'n prop gaan. Dit is belangrik om hier op te let dat die saad voor die eerste gieting van die onderkant af in die vorm ingebring word. Dit vul óf die dwarssnit van die hele vorm, óf slegs die vorm van die werkstuk. Die boonste laag van die saad sal die onderkant van die vorm wees. Daarbenewens het dit ook die vorm van 'n slukstert vir toekomstige koppeling met 'n ingot.
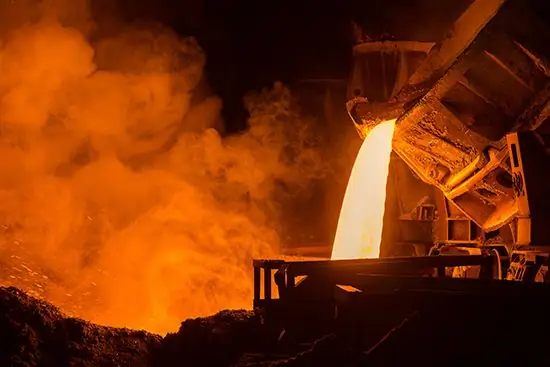
Verdere uitsending
Volgende, in die proses van deurlopende giet van staal, is dit nodig om te wag totdat die vlak van grondstowwe bo die saad styg tot 'n hoogte van ongeveer 300-400 mm. Wanneer dit gebeur, begin die meganisme, wat die trektoestel in werking bring. Dit het trekrolle, onder die invloed waarvan die saad sal val en die geskape staaf daarmee saam trek.
'n Deurlopende gietmasjien het 'n vorm wat gewoonlik van koper gemaak is met hol mure. Hy is onder intensdeur die werking van koelwater, en die interne gedeelte daarvan stem ooreen met die vorm van die ingot wat verkry moet word. Dit is hier waar die ingot-blank kors gevorm word. By hoë gietspoed kan skeur van hierdie kors en lekkasie van metaal voorkom. Om dit te vermy, word die vorm gekenmerk deur heen-en-weer bewegings.
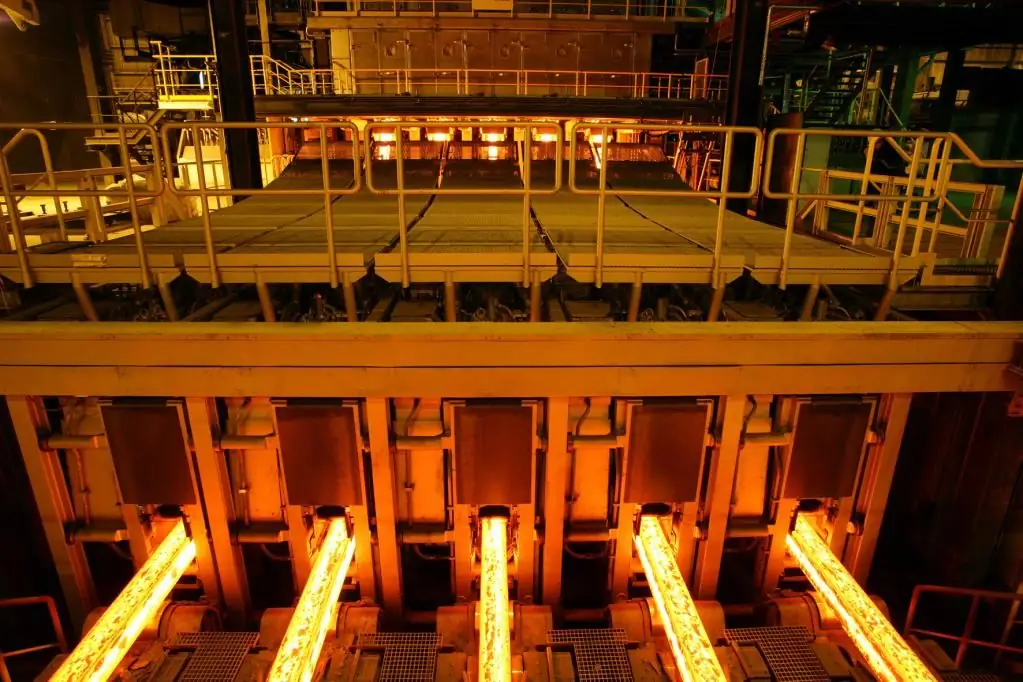
Kenmerke van die vormbewerking
Die deurlopende gietmasjien het 'n elektriese motor wat verantwoordelik is vir die skep van hierdie heen-en-weer beweging. Dit word gedoen deur die krag van die ratkas met 'n nok-tipe swaaimeganisme. Eerstens beweeg die vorm in dieselfde rigting as die werkstuk, dit wil sê af, en nadat die proses voltooi is, keer dit terug na bo. Die swaaislag is van 10 tot 40 mm. Die vorm is 'n belangrike kompartement in die deurlopende giet van staal op enige tipe toerusting, en daarom word sy wande gesmeer met paraffien of enige ander smeermiddel wat geskik is vir die eienskappe.
Dit is opmerklik dat in moderne toerusting die vlak van metaal radiometries beheer word deur 'n beheersein op die skeplepelprop toe te pas. In die vorm self kan óf 'n neutrale óf 'n reducerende atmosfeer bo die metaalvlak geskep word om produkoksidasie tydens produksie te vermy.
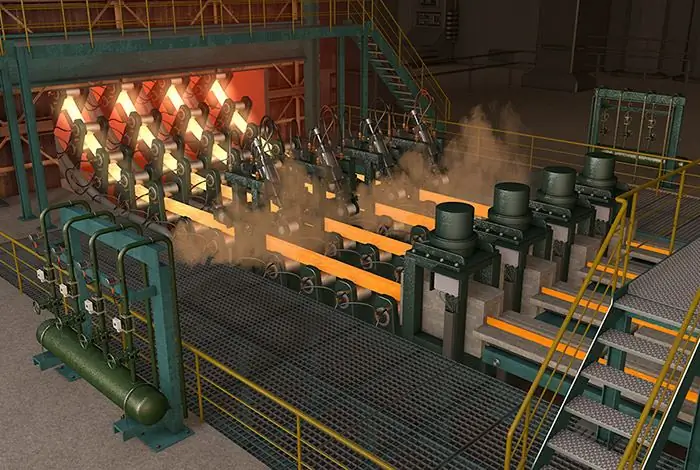
Ingot-skil
Dit is opmerklik dat werk onder vakuum ook as 'n belowende gietmetode beskou word. Een eenheid kan uitvoergooi deur verskeie vorms gelyktydig. Dus kan die aantal strome van een installasie tot agt bereik.
Die hitte sink-aksie van die koue saad word gebruik om die onderkant van die staafvel te vorm. Die ingot sal die vorm verlaat onder die invloed van die saad, wat in die sekondêre verkoelingsone (SCZ) ingetrek word. In die middel van die knuppel sal die staal steeds in 'n vloeibare toestand wees. Dit is belangrik om hier op te let dat, volgens die vereistes van die staalgiettegnologie, die veldikte ten minste 25 mm moet wees ten tyde van die uitgang uit die vorm. Om aan hierdie vereistes te voldoen, is dit nodig om die regte materiaalvloeitempo te kies.
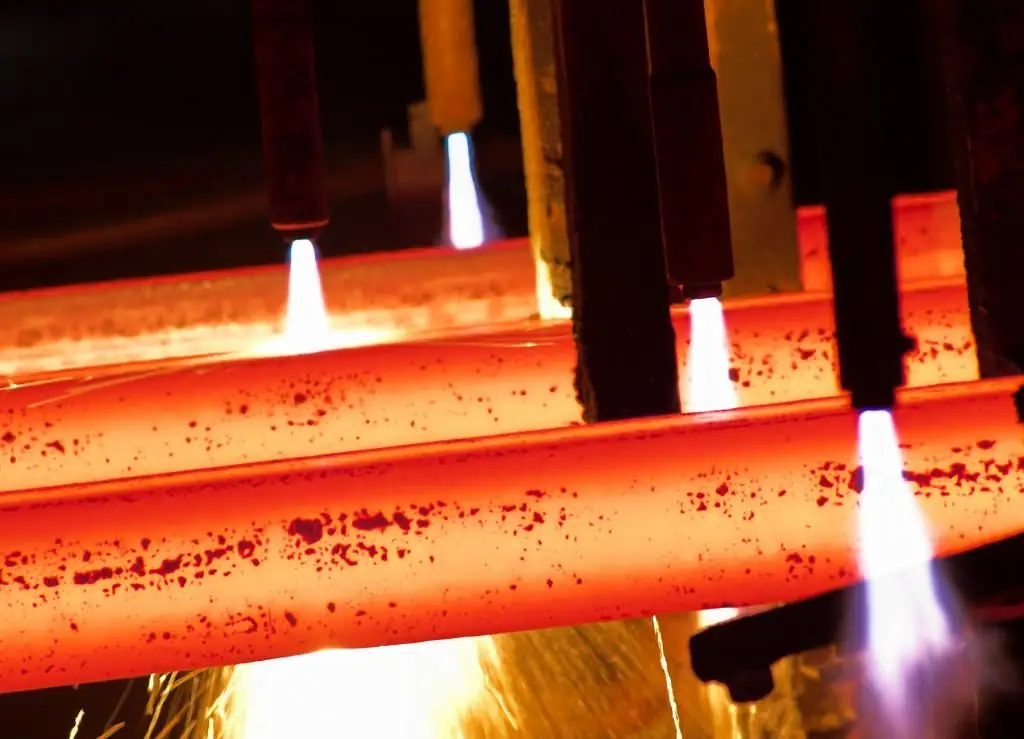
Kenmerke van die installasie- en gietproses
Tegnologiese kenmerke is ongeveer soos volg. As die gedeelte van die staaf 160x900 mm is, moet sy spoed van 0,6 tot 0,9 m/min wees. As die deursnit 180x1000 mm is, word die spoed verminder tot 0,55-0,85 m/min. Die hoogste spoed-aanwyser word benodig vir die deursnit van 'n vierkantige-tipe blok 200x200 mm - 0.8-1.2 m/min.
Gegrond op die bogenoemde aanwysers, kan ons aflei dat die gemiddelde gietspoed van een draad wat deurlopende giettegnologie gebruik, 44,2 t/h is. As jy die optimale spoed oorskry, sal die sentrale porositeit toeneem.
Verder is dit opmerklik dat die stabiliteit van die gietstuk en die kwaliteit van die produk self deur die temperatuur van die metaal beïnvloed word. Empiries is gevind dat by 'n temperatuur van meer as 1560 gradeCelsius is die oppervlak van die staaf dikwels bedek met krake. As die temperatuur laer is as wat aangedui word, sal die glas dikwels styfgetrek word. Daar is dus gevind dat die optimale temperatuur vir die metode van deurlopende giet van staal 1540-1560 grade Celsius sou wees. Om hierdie aanwyser te handhaaf, moet die verhittingstemperatuur van die oond voor vrystelling in die reeks van 1630-1650 grade wees.
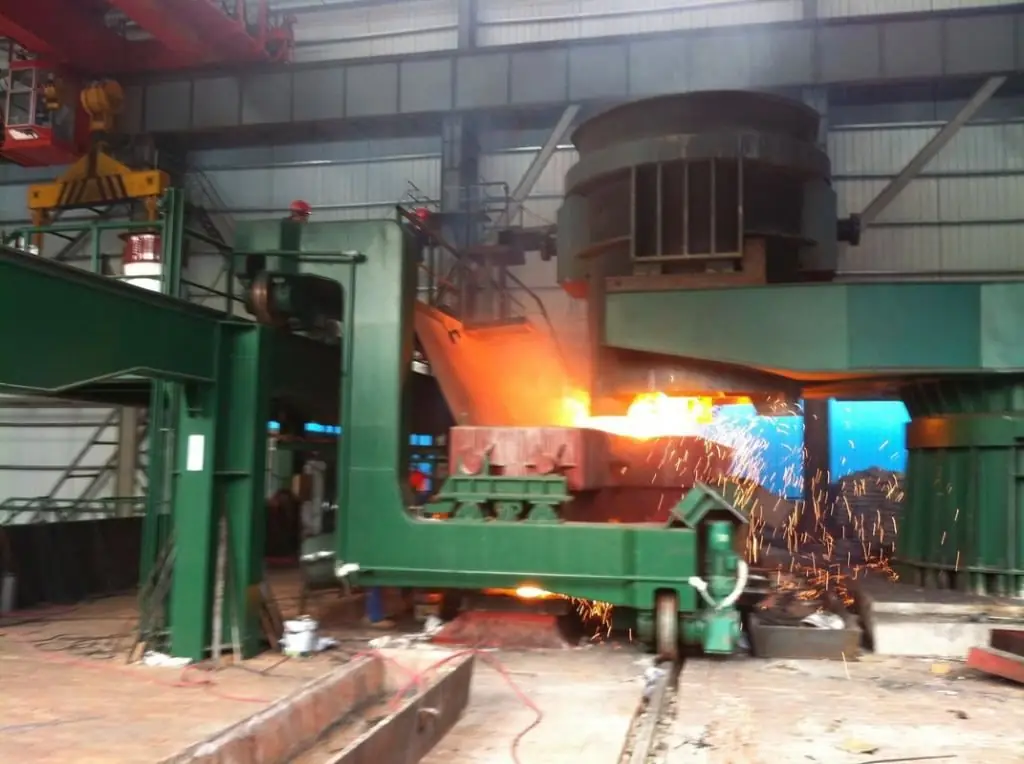
Sekondêre verkoelingsone
In hierdie afdeling word die mees intensiewe en direkte verkoeling van die ingot uitgevoer met behulp van water wat uit die spuitstof kom. Daar is 'n spesiale stelsel van ledige, nie kragrollers nie. Hul rotasie verhoed dat die staaf buig of kromtrek. As gevolg van intense verkoeling in hierdie sone, sal die wande van die staaf vinnig dik word, en kristallisasie sal in diepte versprei. Die spoed om die steen te trek en die mate van afkoeling daarvan moet so gekies word dat teen die tyd dat die steen die trekrolle binnegaan dit reeds heeltemal solied is.
Wat is die voordele van deurlopende casting
Aangesien hierdie metode om staal te giet die metode van giet in vorms vervang het, is dit die moeite werd om met hierdie metode te vergelyk. Oor die algemeen is dit die moeite werd om die volgende voordele uit te lig: groter produktiwiteit, verminderde koste en verminderde arbeidsintensiteit van die proses. As gevolg van die konstante vorming van die ingot word die krimpholte na die stert oorgedra, in teenstelling met die ingot-vorms, waar elke ingot sy eie holte gehad het. As gevolg hiervan neem die persentasie opbrengs van geskikte metaal aansienlik toe. UNRS laat jou toe om te kry'n werkstuk van verskillende vorms, van 'n klein vierkant 40x40 mm tot 'n reghoek 250x1000 mm. Die gebruik van deurlopende gietmasjiene het dit moontlik gemaak om swaaimeulens heeltemal te laat vaar. Dit het die koste van die produksieproses aansienlik verlaag, en dus die prys op die mark. Daarbenewens is die proses van metallurgiese verwerking vereenvoudig.
Flaws
Ondanks die moontlikheid van hoë meganisasie en outomatisering van die proses, 'n hoë persentasie goeie blokke en ander voordele hierbo beskryf, het hierdie metode ook 'n paar negatiewe kante. Die nadele van deurlopende gietstaal is soos volg.
Eerstens is daar geen moontlikheid om blokke van komplekse opset te vervaardig nie. Tweedens is die reeks blokke en spasies redelik beperk. Dit is nogal moeilik om masjiene om te skakel om grondstowwe van 'n ander handelsmerk te giet, wat die finale koste van 'n produk van 'n ander handelsmerk kan verhoog as dit by dieselfde aanleg vervaardig word. Sommige staalgrade, byvoorbeeld kooks, kan glad nie met hierdie metode gemaak word nie.
Die laaste nadeel van die deurlopende metode om staal te giet, is baie beduidend. Dit is 'n moontlike toerusting mislukking. Die mislukking van die UNRS sal tot groot verliese in prestasie lei. Hoe langer dit neem om te herstel, hoe meer verliese sal groei.
Aanbeveel:
Voedselvlekvrye staal: GOST. Hoe om voedselgraad vlekvrye staal te identifiseer? Wat is die verskil tussen voedselvlekvrye staal en tegniese vlekvrye staal?

Die artikel praat oor grade van voedselgraad-vlekvrye staal. Lees hoe om voedsel vlekvrye staal van tegniese te onderskei
Rookwinkel: voorbereiding van nodige dokumente, opstel van 'n sakeplan, keuse van nodige toerusting, doelwitte en stadiums van ontwikkeling
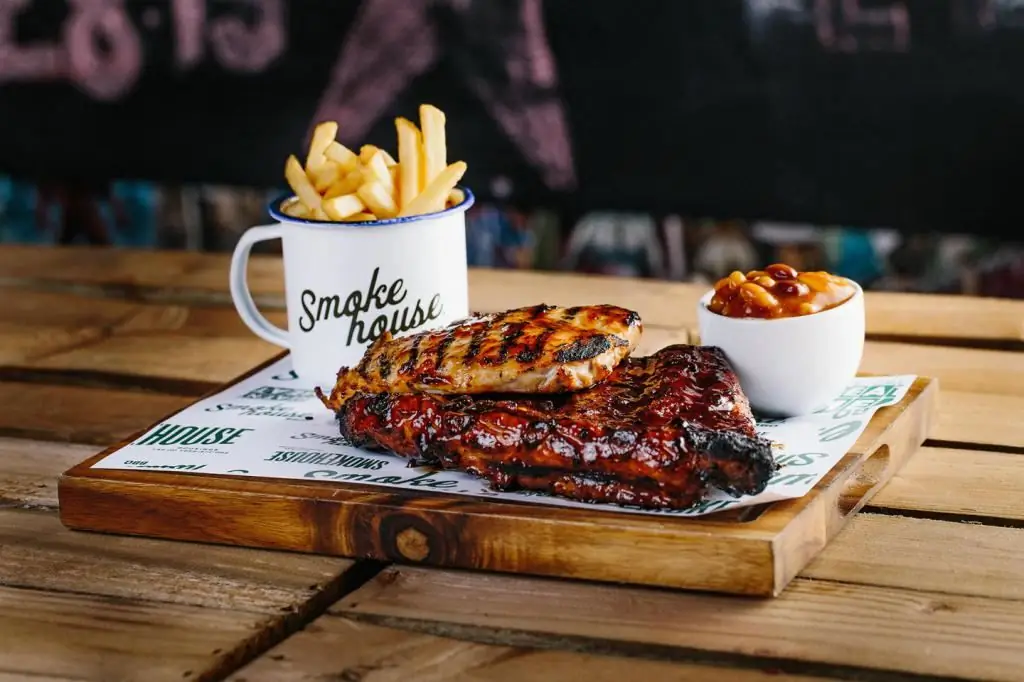
Die artikel handel oor so 'n besigheid soos 'n rookwinkel. Leer hoe om 'n besigheid te begin en waar om te begin. Oor hoe om toerusting te kies en hoe dit moet wees. Oor wat jy moet let op wanneer jy verskaffers kies, en oor die proses om gerookte produkte te vervaardig
Haarkapper by die huis: voorbereiding van nodige dokumente, opstel van 'n sakeplan, keuse van nodige toerusting, doelwitte en stadiums van ontwikkeling
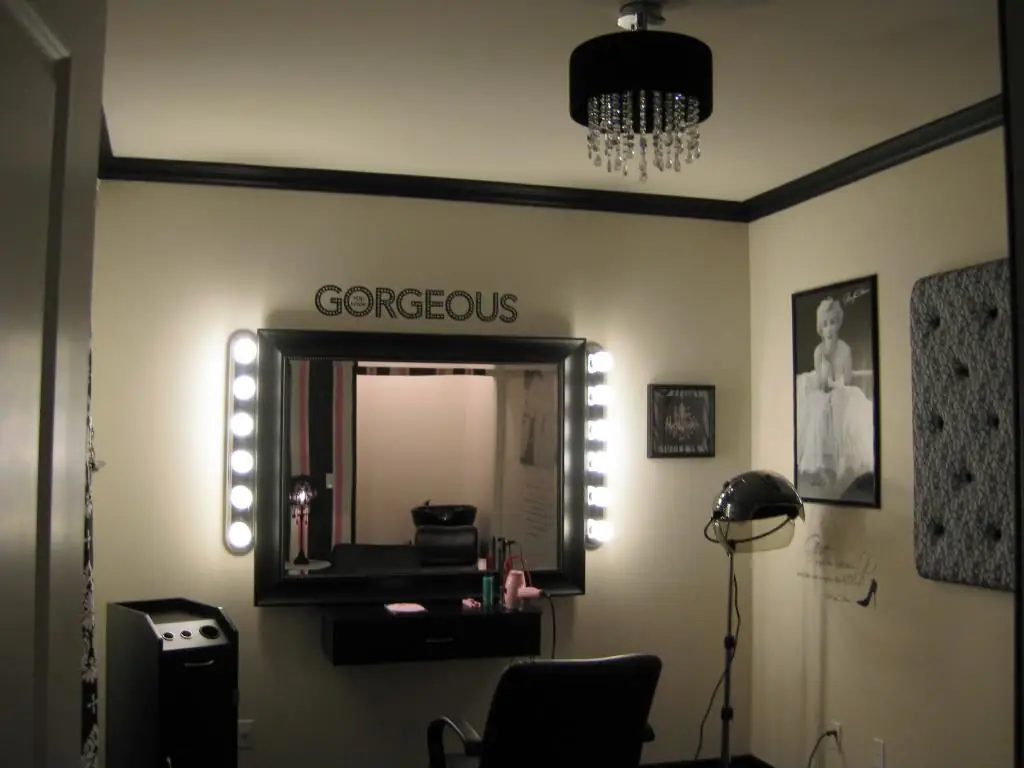
Haarkappersonderneming vir kreatiewe mense is 'n baie belowende en interessante besigheid. Wel, as daar nie geld is om 'n groot salon oop te maak nie, is dit aanvanklik heel moontlik om jou projek van die eerste fase af te begin. Hiervoor kan 'n haarkappersalon by die huis georganiseer word, wat nie groot beleggings verg nie. Is dit die moeite werd om by so 'n besigheid betrokke te raak, en watter stappe sal jy moet deurgaan om dit oop te maak?
Giet in silikoonvorm: toerusting. Vakuum giet in silikoon vorms
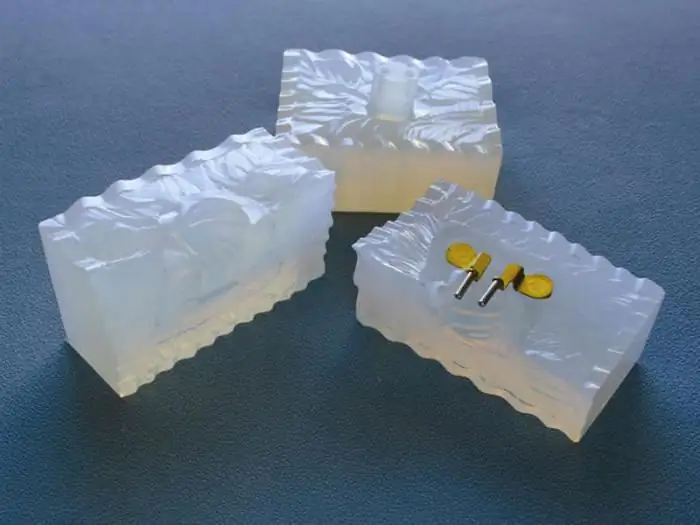
Vir die vervaardiging van 'n klein aantal spasies van plastiek word vakuumgiet in silikoonvorms die meeste gebruik. Hierdie metode is redelik ekonomies (om 'n metaalvorm te maak verg meer tyd en geld). Daarbenewens word silikoonvorms herhaaldelik gebruik, en dit verminder ook die produksiekoste aansienlik
Diesel duikbote: geskiedenis van skepping, bootprojekte, beginsel van werking, voordele, nadele en stadiums van ontwikkeling
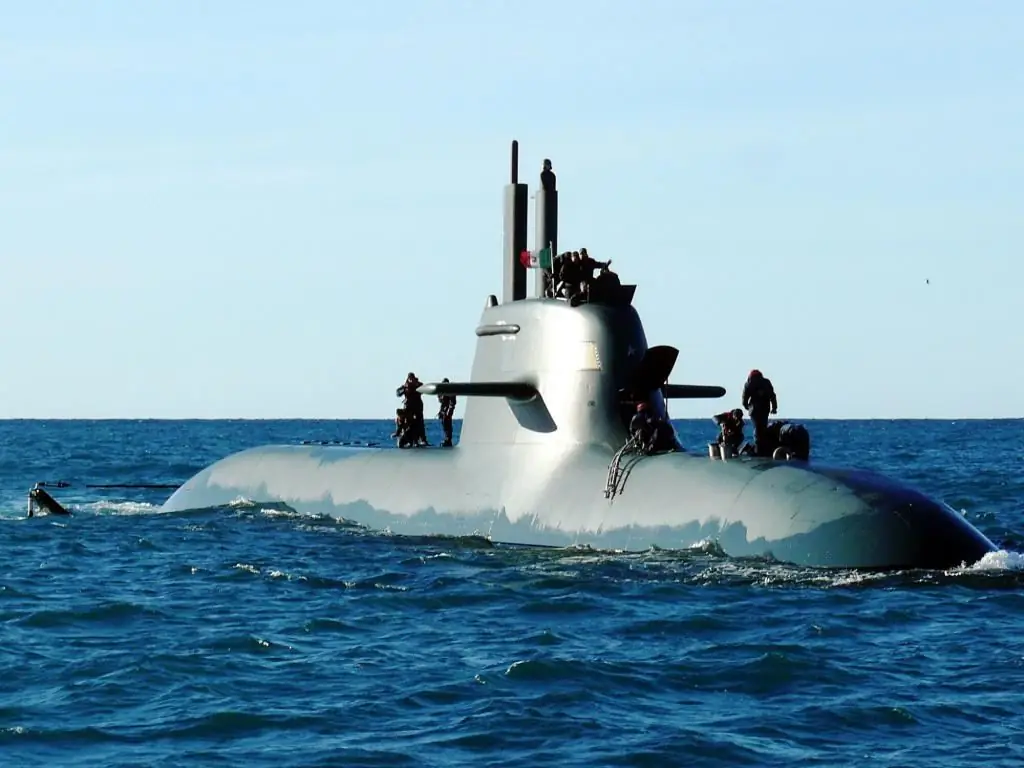
Die idee om 'n duikboot te skep wat onder water beweeg, eintlik 'n prototipe van 'n duikboot (hierna na verwys as 'n duikboot), het ontstaan lank voor hul werklike verskyning in die 18de eeu. Daar is geen presiese beskrywings van onderwatervoertuie in talle legendes nie, ook nie in die Renaissance-genie Leonardo da Vinci nie