2025 Outeur: Howard Calhoun | [email protected]. Laas verander: 2025-01-24 13:11
Giet in dopvorms word ook dopgiet genoem. En in die buiteland word hierdie werkswyse Shell genoem.
Algemene inligting
In vandag se industriële industrie word baie verskillende gietmetodes gebruik. Benewens dopgietwerk word beleggingsgietwerk ook gebruik, asook in metaalvorms en verskeie ander metodes. Die algehele voordeel van hierdie gietmetodes, in vergelyking met sandgietwerk, is dat dit meer akkurate eindmateriale in terme van vorm sowel as afmetings tot gevolg het. Daarbenewens word die aantal ruwhede op die oppervlak van sulke produkte verminder. In meer seldsame gevalle, maar tog gebeur dit dat die behoefte aan daaropvolgende bewerking na smelting uitgeskakel word. Benewens alles, dra die gebruik van gietwerk in dopvorms en ander metodes daartoe by dat hierdie proses soveel moontlik gemeganiseer kan word, waardeur die outomatisering daarvan ook toeneem. En dit verhoog natuurlik die produktiwiteit van enige industriële fasiliteit aansienlik.
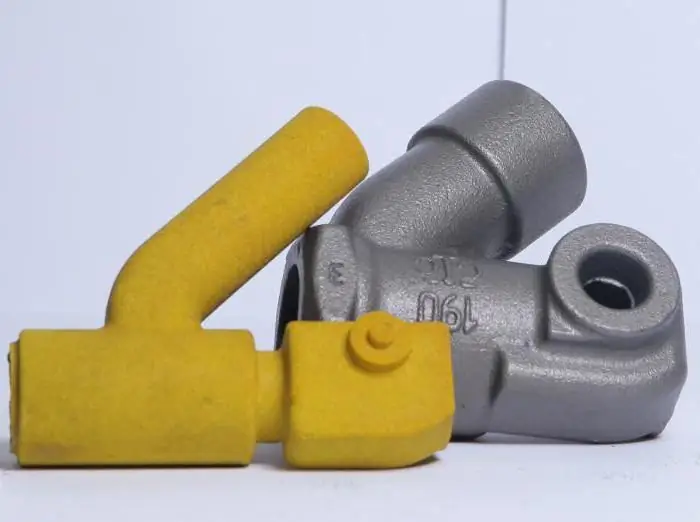
Shell-uitsaaiery
As ons spesifiek hieroor praatmetode, is dit die eerste keer in 1953 by fabrieke bekendgestel. Tans word die metode redelik wyd gebruik. Dit is byvoorbeeld giet in dopvorms wat die meeste van die onderdele vir die Kirovets-trekker vervaardig. Alle onderdele wat met hierdie metode vervaardig word, is van die hoogste geh alte van staal of gietyster. Dopgietwerk is 'n metode waarin die finale resultaat van die gietwerk 'n vorm het wat uit twee sand-harsdoppe bestaan. Hierdie metode om onderdele te vervaardig word ook slegs gebruik in gevalle waar dit nodig is om 'n onderdeel met klein of medium afmetings te skep, maar terselfdertyd met hoë akkuraatheid. Voorbeelde van toepassings vir hierdie gietmetode is enjinonderdele of dunwandgietstukke.
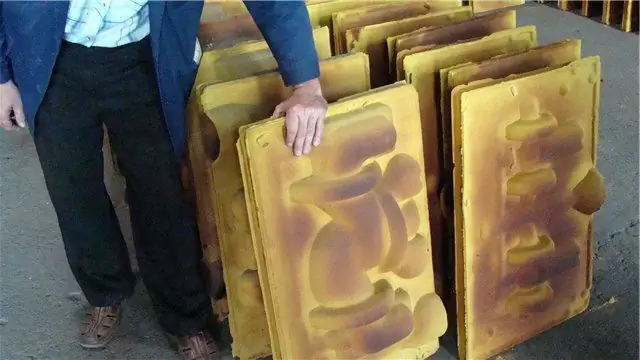
The Essence of the Way
Met hierdie werkmetode kan jy verskeie onderdele vir waaiers, motors, pompe of tekstielmasjiene kry. Die maksimum lengte van die produk wat ontvang word, kan egter nie 1 meter oorskry nie, en dit kan nie swaarder as 200 kg wees nie.
Die kern van giet in dopvorms is gebaseer op sekere eienskappe van termohardende harse, wat deel is van sand-hars-mengsels. Die voordeel van die gebruik van sulke komponente is dat hierdie harse geneig is om vinnig en permanent te verhard wanneer dit met 'n temperatuur van 200-250 grade Celsius behandel word.
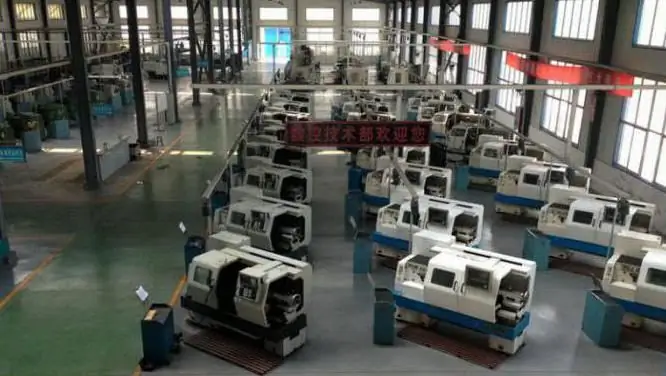
Maak 'n dopvorm vir giet
Om 'n vorm te maak vir daaropvolgende gietwerk, is dit nodig om fynkorrelige kwartssand te hê, wat gepaard gaan met die byvoeging van 'n termohardende hars, wat die verbindingselement daarvan is om 'n volwaardige dopvorm te verkry. Hierdie materiale, veral die hars, word gekies omdat hulle hard word wanneer hulle 'n sekere temperatuurversperring verbysteek. Die vervaardigingsproses is soos volg. Eerstens word die hars verhit tot 140-160 grade Celsius. Onder die invloed van so 'n omgewing verander dit in 'n vloeibare kleefmassa wat die kwartssandvorm heeltemal omvou.
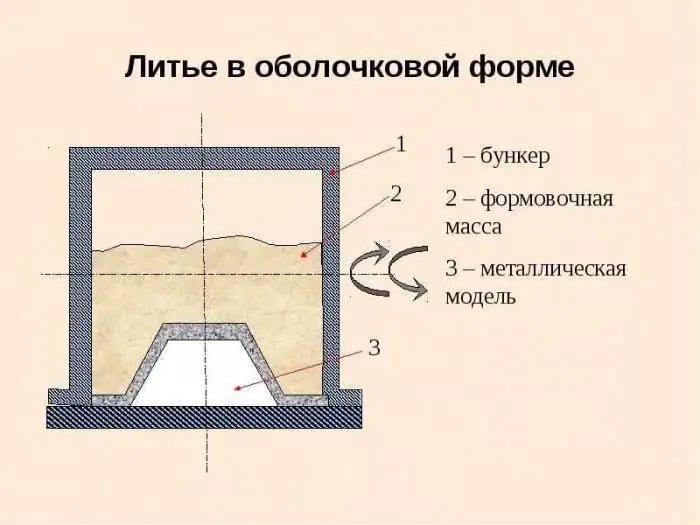
Die omvang van giet in dopvorms is redelik wyd, en daarom word die proses om vorms te maak na outomaties of outomaties gebring.
Nadat die vorm heeltemal bedek is met hars, word die temperatuur verhoog na 200-250 grade Celsius. Hierdie temperatuurdrempel is heeltemal genoeg vir die kleefmassa om onomkeerbaar hard te word en 'n vorm te vorm. Verder, wanneer die proses van die giet van dele begin, dit wil sê wanneer die gesmelte metaal die vorm binnedring, bereik die temperatuur daarin ongeveer 600 grade. Hierdie modus is genoeg om te verseker dat die hars nie smelt nie, maar uitbrand, terwyl dit porieë op die vorm self laat, wat die ontsnapping van gasse vergemaklik.
Voor- en nadele van dopvormgietwerk
Soos enige ander vervaardigingsproses, het hierdie een sy voor- en nadele. As ons hierdie metode van ingieting vergelyk, byvoorbeeld met ingietgewone sandvorms, daar is verskeie voordele:
- Die eerste en nogal beduidende verskil is die akkuraatheidklas, wat 7-9 is. Daarbenewens word die oppervlakafwerking van die verkryde deel verbeter tot 3-6. Daarbenewens word toelaes verminder, wat toegelaat word vir die daaropvolgende bewerking van die resulterende deel na giet.
- Een van die groot pluspunte is 'n aansienlike vermindering in arbeidskoste vir die vervaardiging van gietstukke.
- Hierdie gietmetode verminder die verbruik van gietmateriaal, sowel as die hoeveelheid metaal as gevolg van die feit dat die grootte van die hekkanale verminder word.
- Verminder die hoeveelheid huweliksuitset aansienlik.
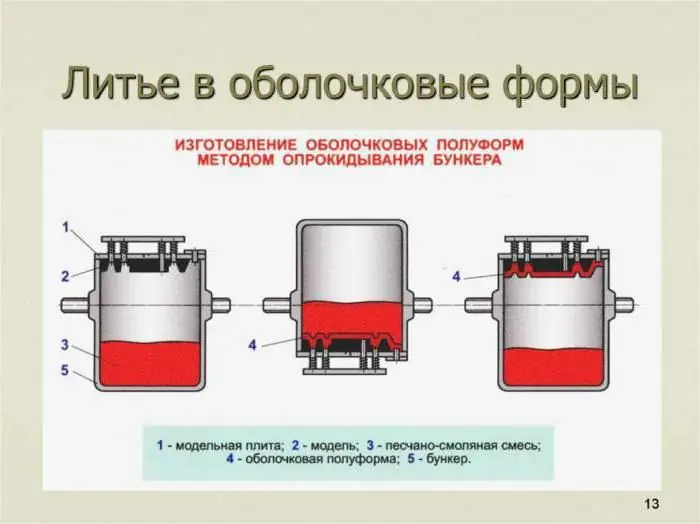
Daar is egter 'n paar nadele om in dopvorms te giet. Dit sluit in:
- Dopvormlewe - 1 gietstuk.
- Die koste om sand te giet is redelik hoog.
- Hoë persentasie skadelike gasse.
Korpusvormingsproses
Die liggaamsvormingsproses word in ses fases uitgevoer:
- Die eerste stap is die proses om die mengsel op 'n warm metaalmodel te gooi, asook die proses om dit vir 'n paar tientalle sekondes te hou totdat 'n dun, sterk kors om die deel vorm. Dikwels word modelle van gietyster gemaak, en hul verhitting word uitgevoer tot 230-315 grade.
- Daarna is dit nodig om 'n operasie uit te voer om oortollige vormsand te verwyder. Die dikte van die kors moet uiteindelik van 10 tot 20 weesmm. Dit hang af van die verblyftyd van die mengsel op die model, asook van die temperatuur.
- Daarna is dit nodig om die modelplaat saam met die vorm oor te dra na die oond, waar hulle sal wees tot aan die einde van die uithardingsproses. Aan die einde van hierdie prosedure moet die sterkte van die dop tussen 2,4 en 3,1 MPa wees.
- Nadat dit uit die oond verwyder is, word die verharde dop van die plaat verplaas. 'n Spesiale drukker word vir hierdie prosedure gebruik.
- Daarna word twee of meer modelle aanmekaar vasgemaak met behulp van een of ander klamp of deur gom. Hierdie vorms kan gebruik word om in dopvorms te giet of eenvoudig gestoor word. Byna onbeperkte raklewe.
- Voordat die gietproses in die voltooide vorm begin word, word skoot daarin gegooi, wat help om die vorm te voorkom of te vernietig tydens verdere giet.
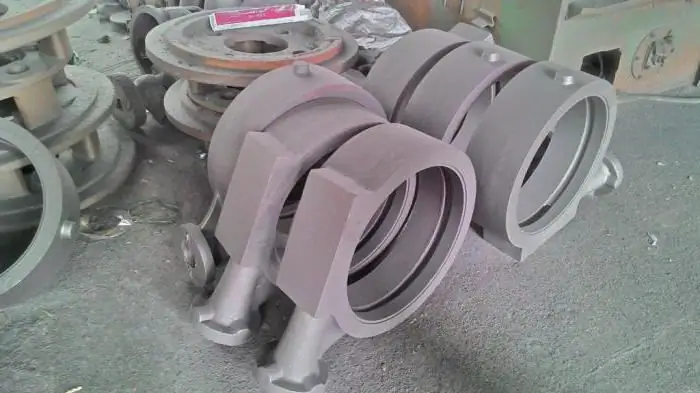
Uitsaaibesonderhede
Dit is die moeite werd om te begin met die feit dat tipiese toleransies wat toegelaat word in die vervaardiging van gereedskap 0,5 mm kan wees. Oppervlakgrofheid word toegelaat in die reeks van 0,3 tot 0,4 mikron. Sulke perke word geregverdig deur die feit dat fynkorrelige sand gebruik word. Ook opmerklik: die gebruik van hars dra grootliks by tot die feit dat die oppervlak baie glad is.
Produksievolumes
Om by die vervaardiging van sulke vorms en onderdele betrokke te wees, is dit nodig om aandag te gee aan die installering van 'n vormmodel. Die tyd wat nodig is vir installasie is minder as 'n week. Nadat die installasie voltooi is, kan die uitsethoeveelheidbereik van 5 tot 50 stukke per uur. Sulke produksievolumes per uur is redelik werklik, maar hiervoor is dit nodig om die gietproses dienooreenkomstig voor te berei. Die belangrikste materiale wat vir gietwerk benodig sal word, is gietyster, aluminium, koper, sowel as legerings van hierdie tipe metale. Nog 'n noodsaaklike materiaal sal 'n legering wees wat aluminium en magnesium gebruik.
Aanbeveel:
Die strategiese beplanningsproses sluit in Stappe en basiese beginsels van strategiese beplanning
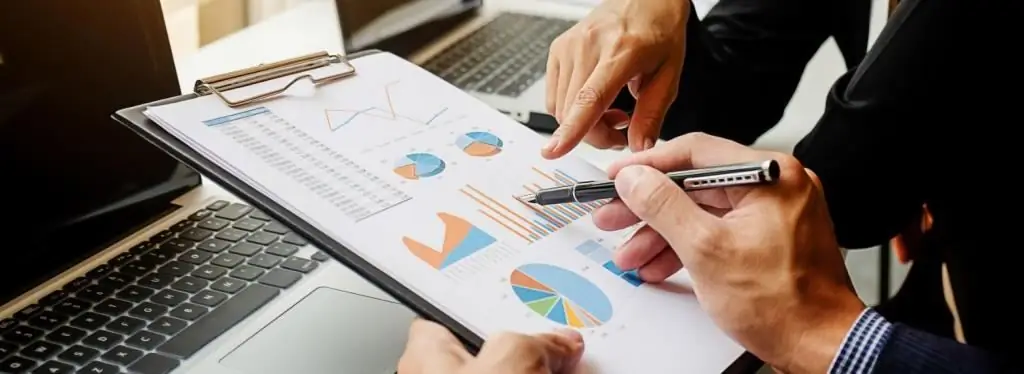
Op baie maniere bepaal die sukses van die maatskappy in die mark die strategiese beplanning in die organisasie. As 'n metode is dit 'n stap-vir-stap studie en tegniek om 'n prosedure uit te voer wat gemik is op teoretiese en praktiese konstruksie van 'n model van die maatskappy se toekoms. 'n Duidelike program vir die oorgang van 'n organisasie of onderneming na 'n optimale bestuursmodel in die mark
Finansiële hulpbronne van kommersiële organisasies: basiese konsepte, tipes, bronne van vorming
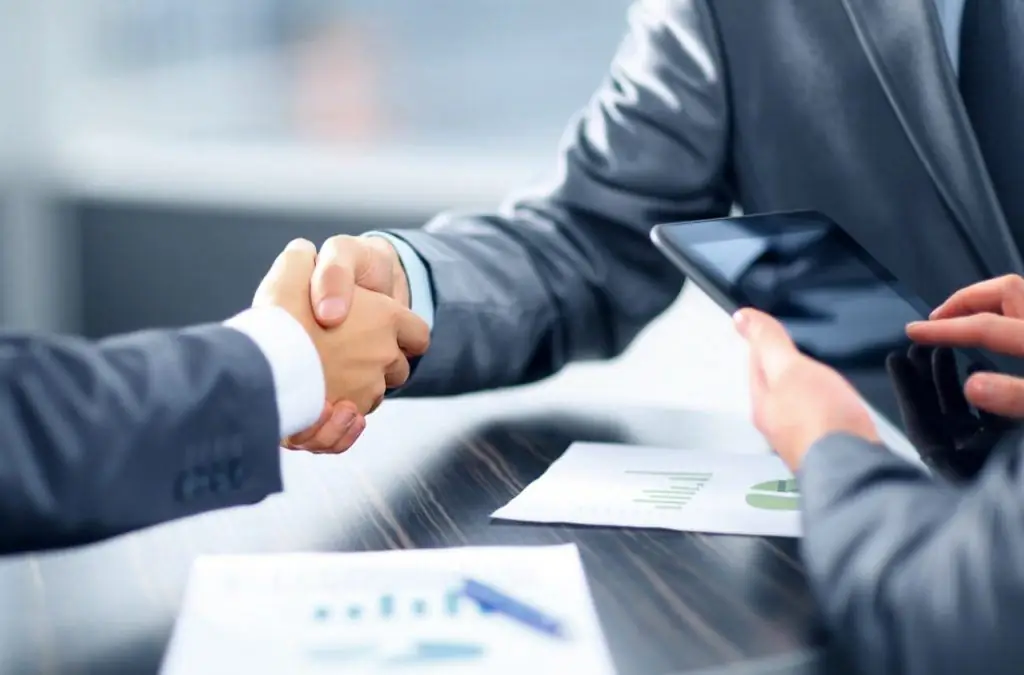
Die leerstelling van finansiële hulpbronne in ons staat is die eerste keer in 1928 ingestel, toe die ontwikkelingsdoelwitte van die USSR vir die tydperk van 1928 tot 1932 bepaal is. Op die oomblik is daar geen enkele presiese definisie van hierdie konsep nie, wat geassosieer word met die praktiese diversiteit van die konsep. Daar is 'n groot hoeveelheid finansiële hulpbronne van kommersiële organisasies en hul samestellings, daarom gee verskillende ekonome die konsep verskillende definisies
Gemoedsbestuur: konsep, definisie, basiese beginsels en tematiese boeke
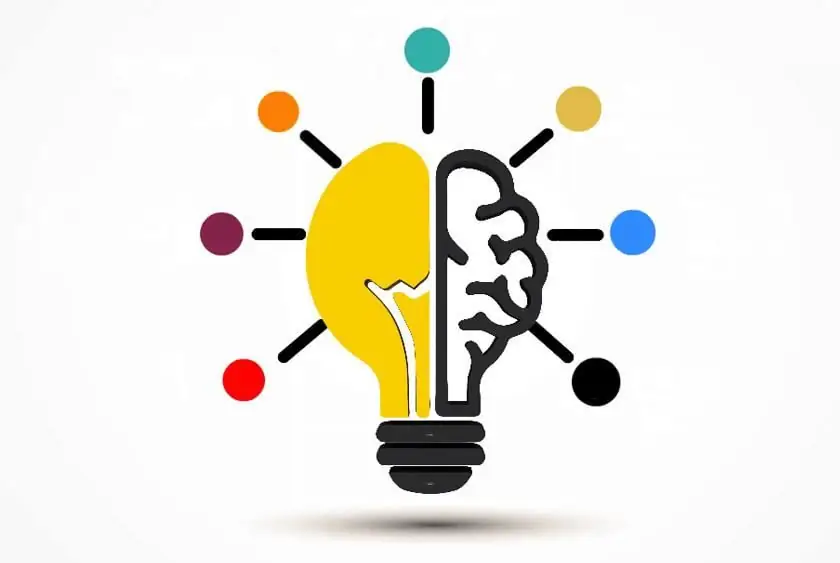
Min moderne mense weet hoe om hul tyd te bestuur. Ten spyte van die gewildheid van tydsbestuur, verdwaal mense in die vloei van inligting, en hulle kan nie daarin slaag om hul lewens reg te maak nie. En al hoekom? Om die rede dat hulle nie 'n enkele stelsel vir die strukturering van inligting het nie. Geestesbestuur sal jou help om orde in ewige chaos te bring
Talentbestuur: konsep, basiese beginsels, personeelbeleid en ontwikkelingsprogramme

Hierdie artikel word gewy aan die oorweging van die talentbestuurstelsel. Die inligting verskaf 'n gedetailleerde beskrywing van die talentbestuurstrategie by die onderneming, sy basiese beginsels en stadiums van werk met personeel
Porter se strategieë: basiese strategieë, basiese beginsels, kenmerke
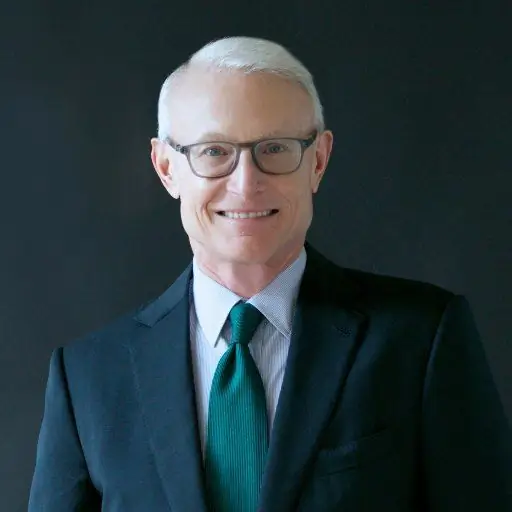
Michael Porter is 'n bekende ekonoom, konsultant, navorser, onderwyser, dosent en skrywer van talle boeke. wat hul eie kompetisiestrategieë ontwikkel het. Hulle neem die grootte van die mark en kenmerke van mededingende voordele in ag. Hierdie strategieë word in die artikel uiteengesit